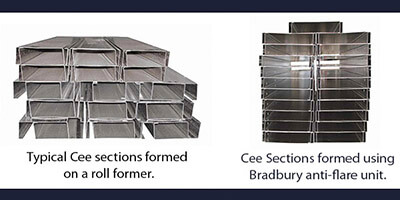
2 min read
FAQ: How is End Flare controlled in Roll Formed Profiles?
End flare can be inherent in roll formed parts, especially when produced on a precut roll forming line as opposed to a post cut line which forms the panel first and then shears it to length. The amount of flare depends on the tooling design, the use...
Read More