1 min read
Read the latest News From The Bradbury Group
Company News
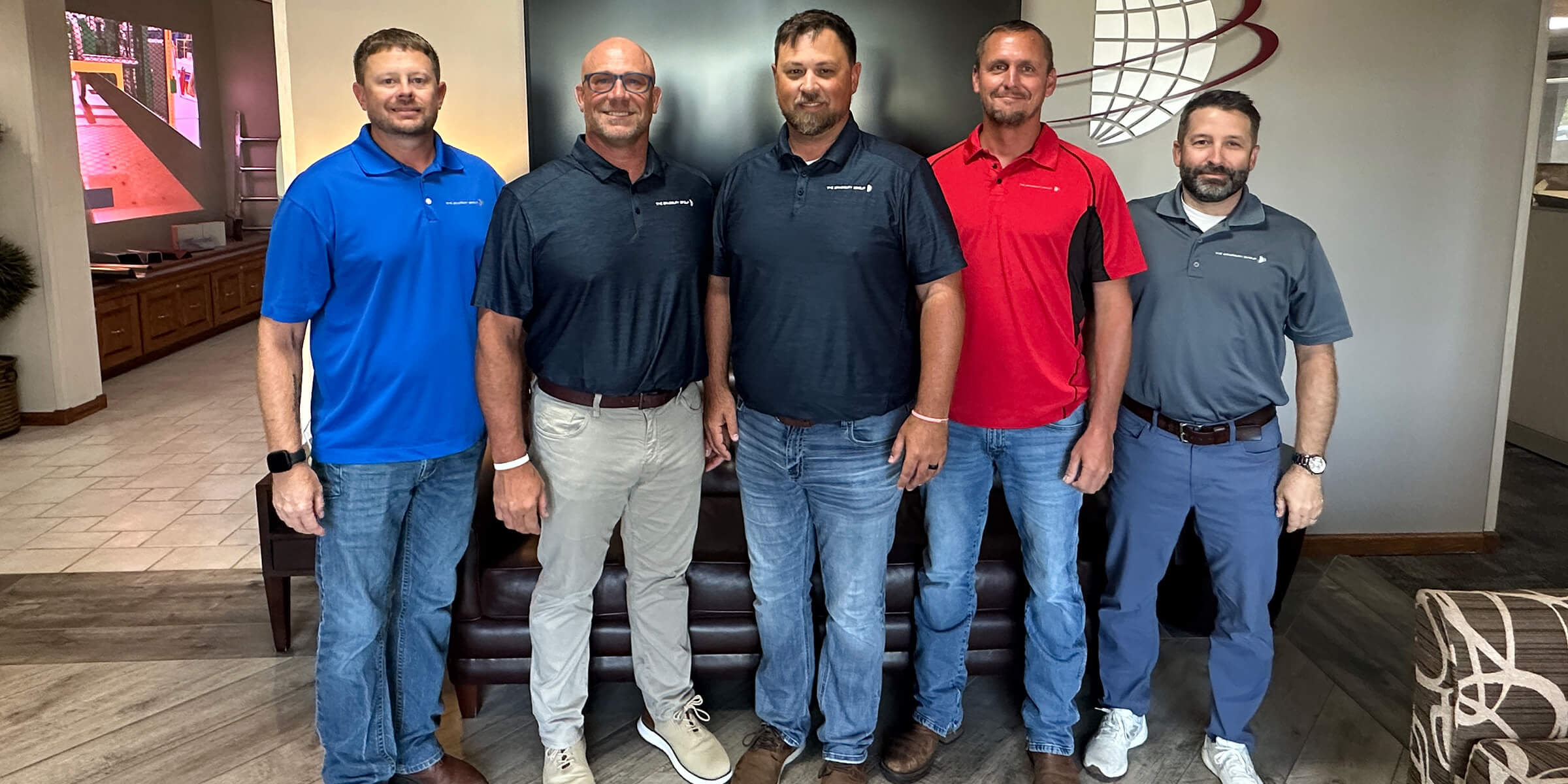
1 min read
Driving Operational Excellence: Leadership Transition at Bradbury
At Bradbury, our ongoing mission is to deliver world-class solutions with greater speed, precision, and reliability. Over the past several years, we...
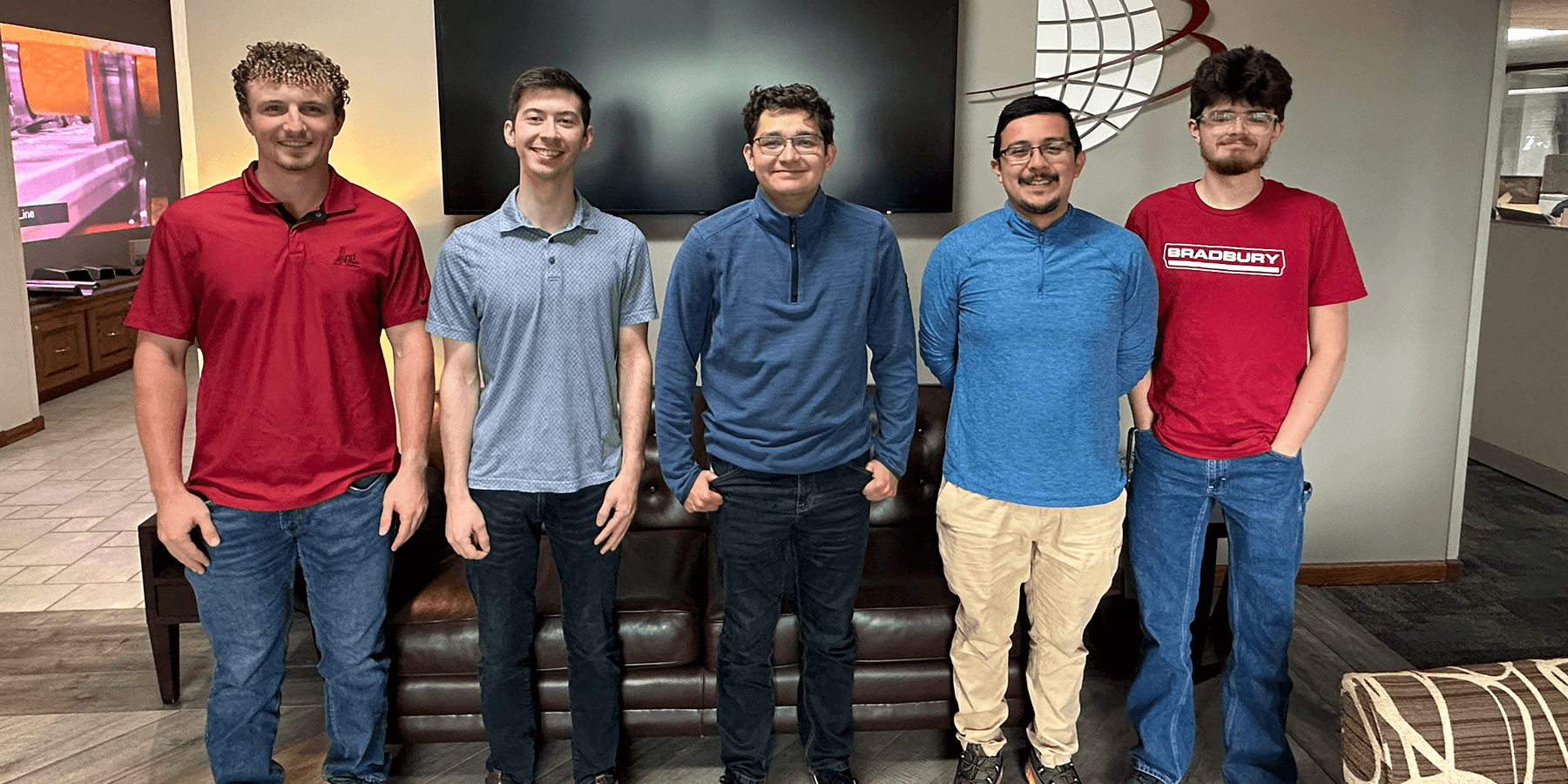
1 min read
Bradbury Welcomes Its 2025 Summer Interns
Bradbury is proud to welcome a talented group of new and returning students to our facility this summer. Whether working on manufacturing processes...

1 min read
Bradbury Hosts Annual Charity Golf Tournament to Support Local Fire Departments
Despite the heavy rains Kansas has seen lately, The Bradbury Group hosted its annual charity golf tournament on Friday, May 30th, bringing together...
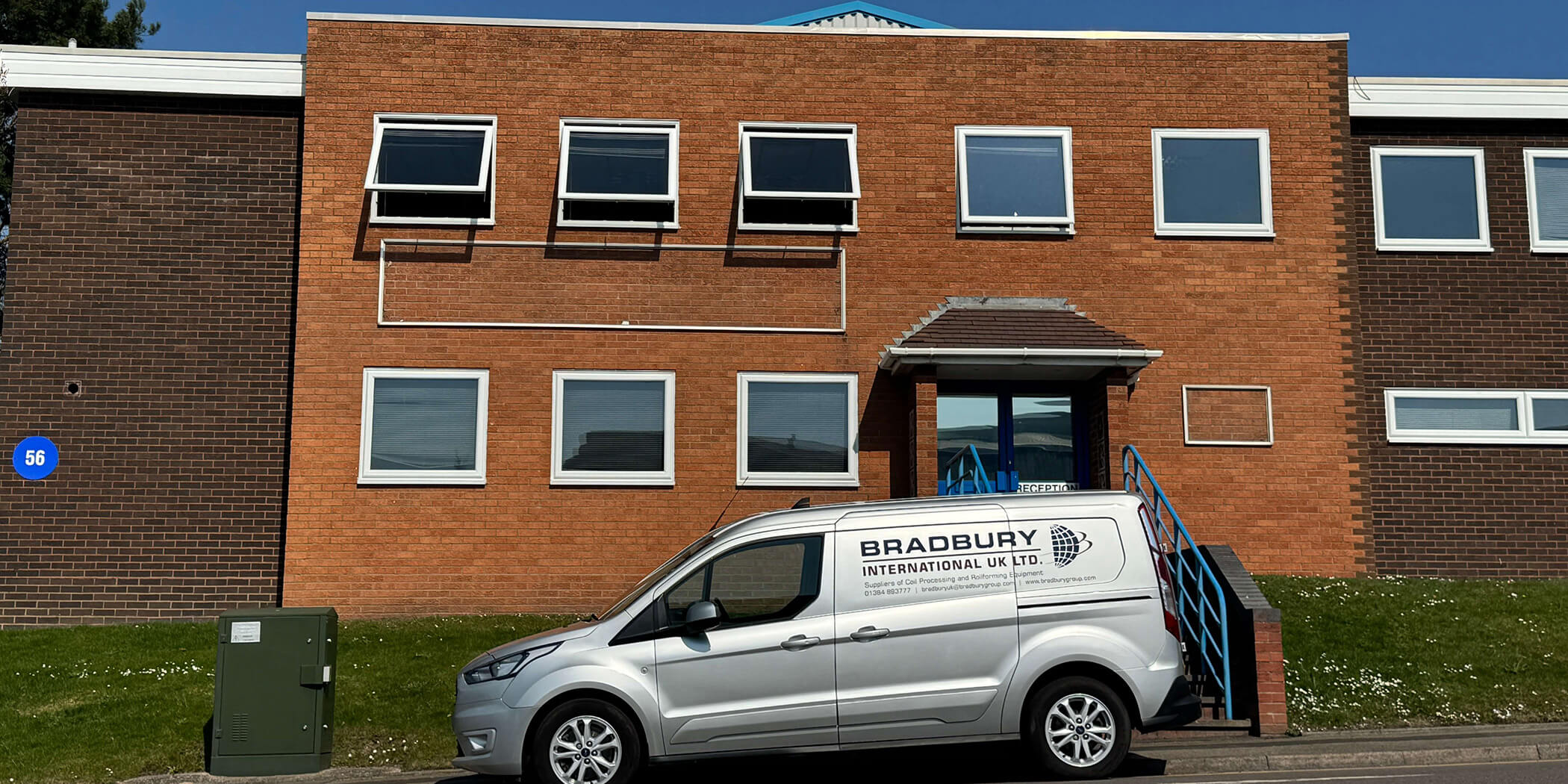
1 min read
Bradbury International UK Ltd is Relocating to a Larger Facility
Bradbury International UK Ltd is pleased to announce that we are relocating to a new facility that includes manufacturing space. The new facility...
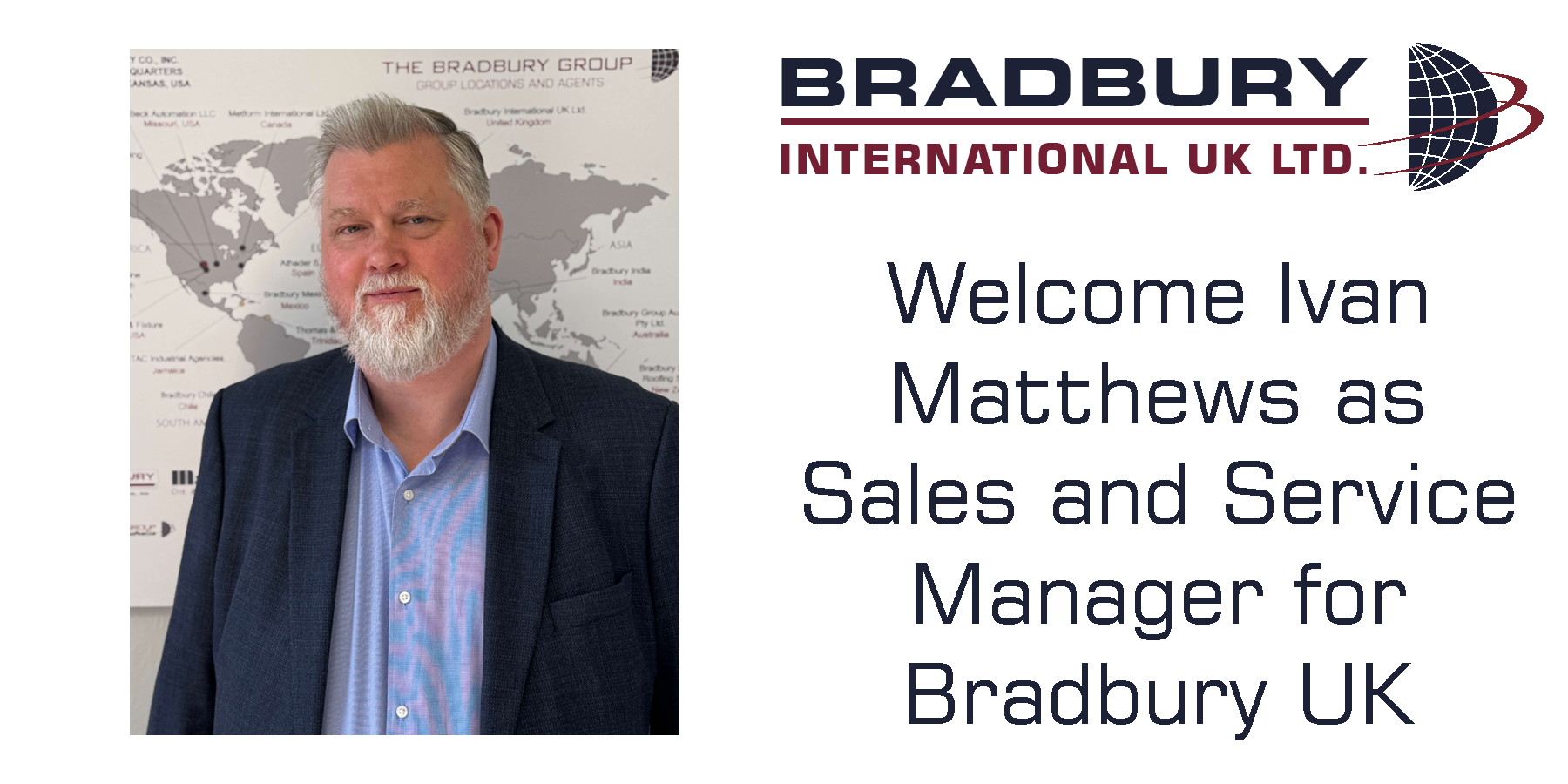
1 min read
Bradbury International UK Ltd Welcomes Ivan Matthews as Sales and Service Manager
Bradbury International UK Ltd is delighted to welcome Ivan Matthews as the newest addition to our growing team. Ivan joins us in the role of Sales...
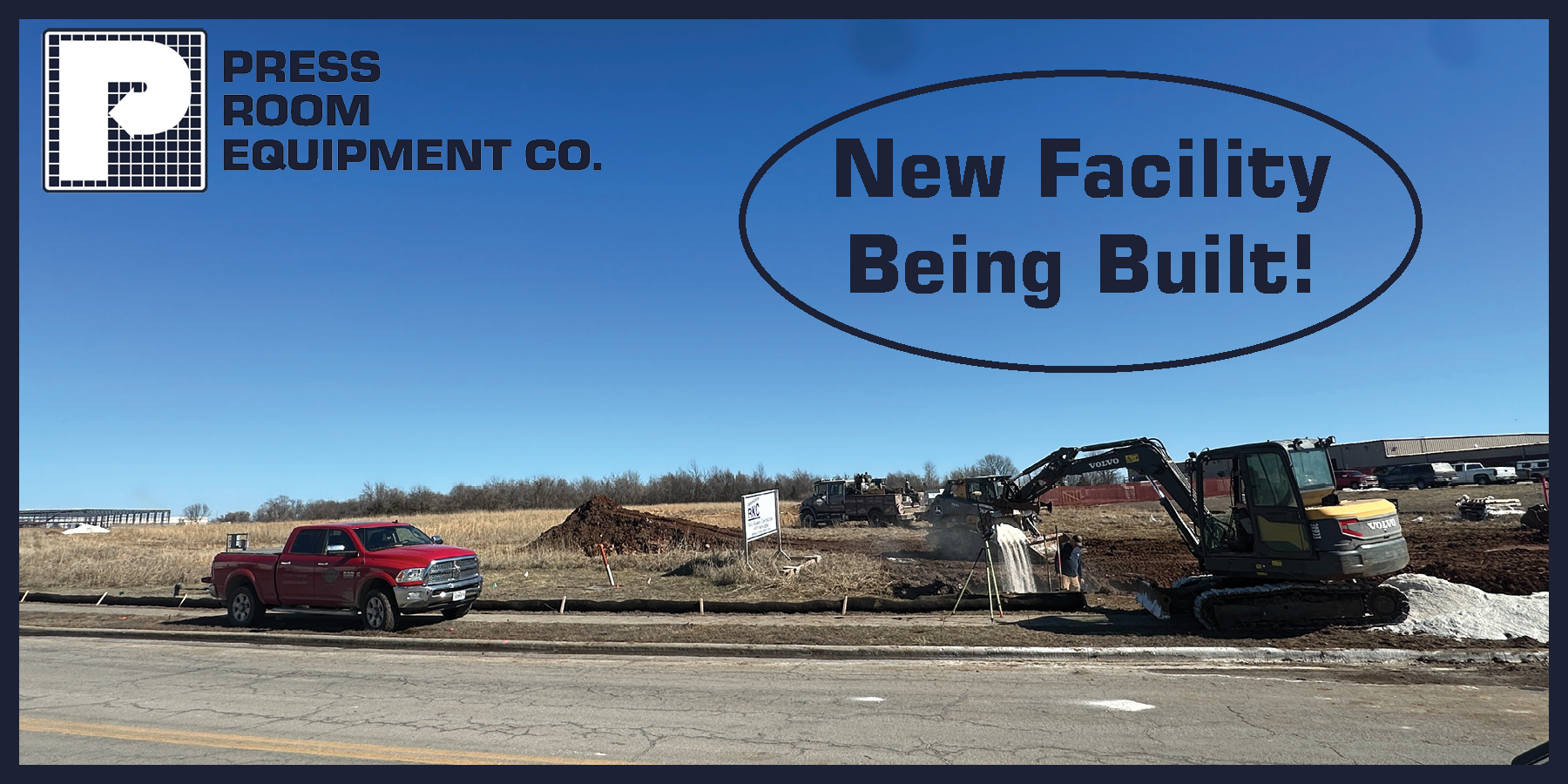
2 min read
Press Room Equipment Is Expanding with a New Facility
Press Room Equipment Co. (PRE) was founded in the late 1970s in Rhode Island, starting as a small company with a focus on providing high-quality...
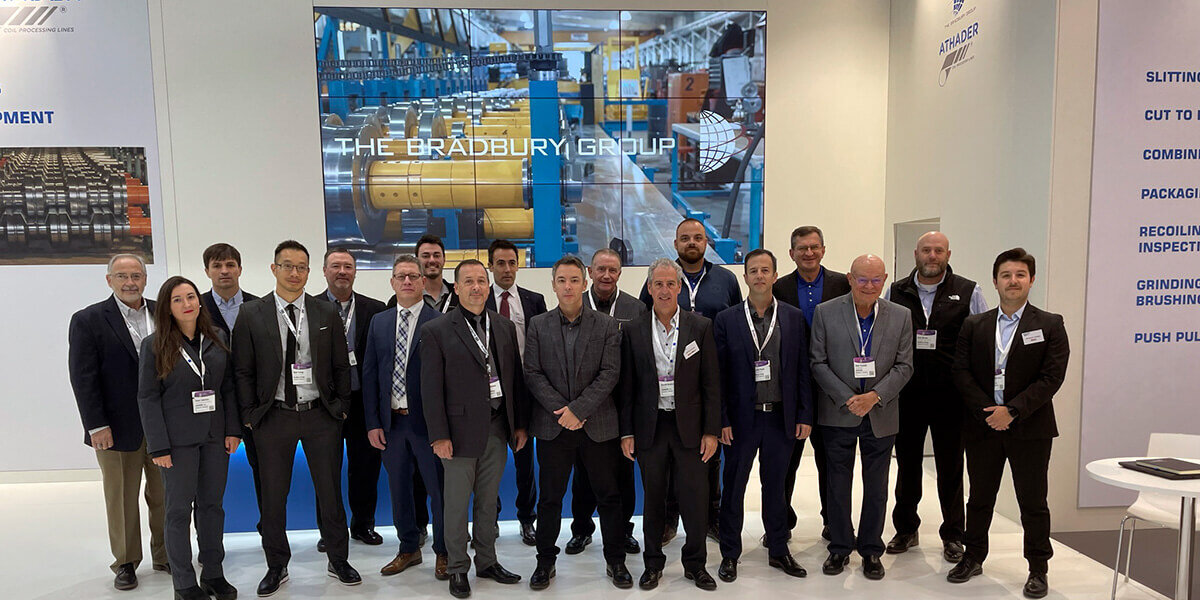
2 min read
Join The Bradbury Group at Upcoming 2025 Tradeshows
The Bradbury Group is excited to announce our participation in several upcoming 2025 tradeshows and conferences. We look forward to showcasing our...
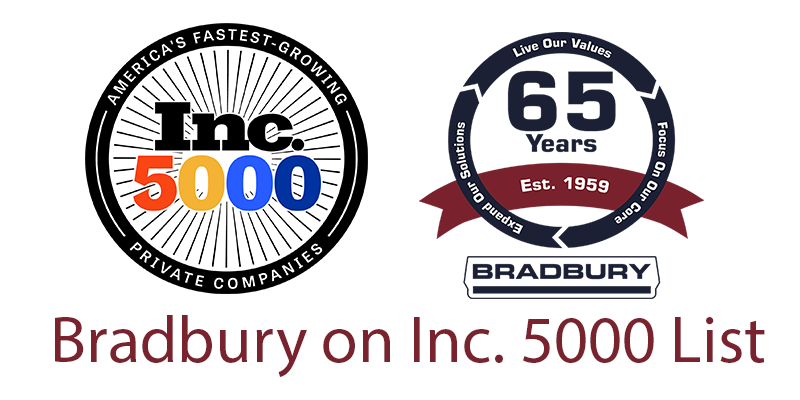
2 min read
Bradbury on Inc. 5000 List of Fastest Growing Private Companies
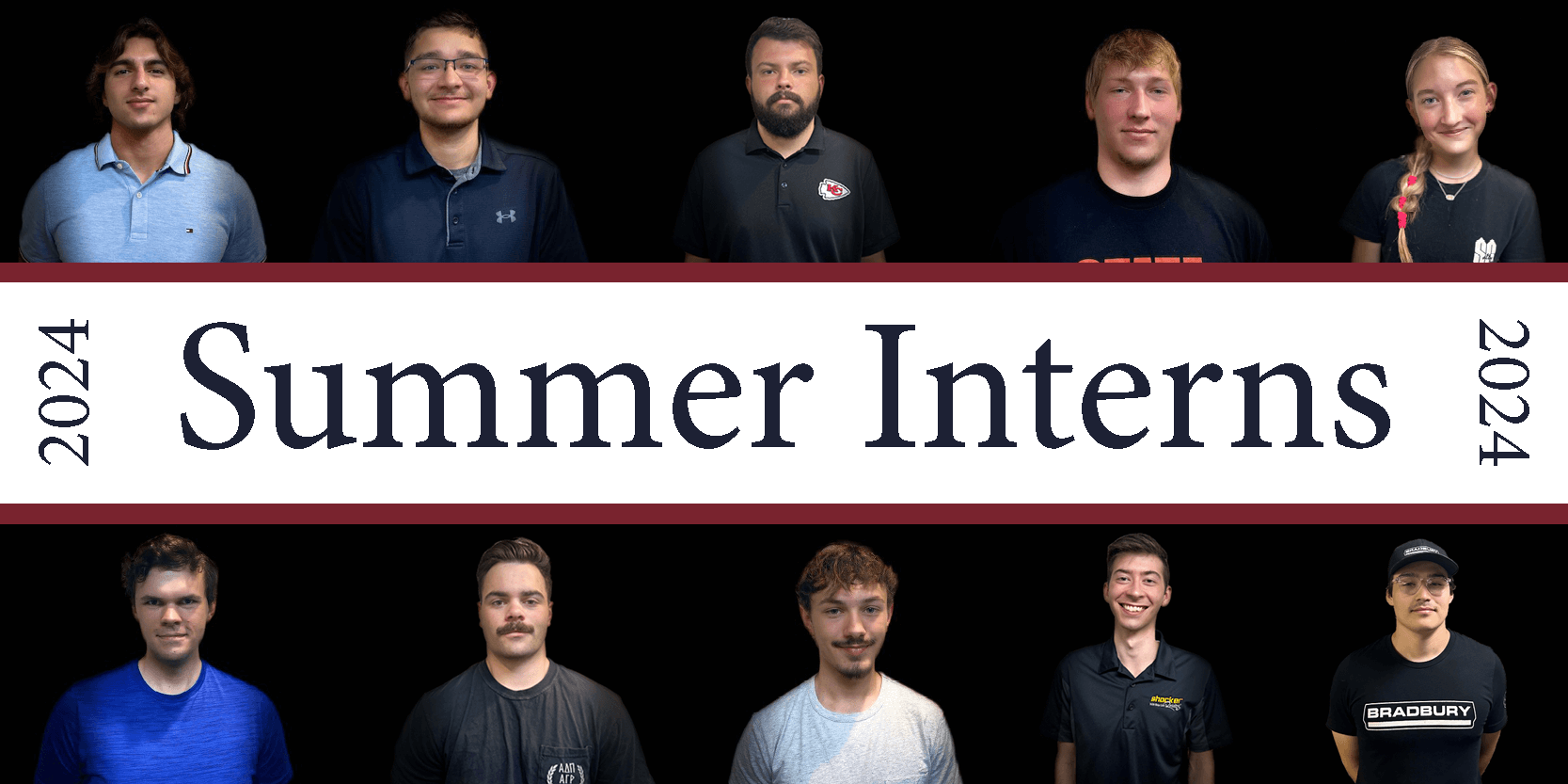
2 min read
Bradbury Welcomes Ten Summer Interns to the Team
Bradbury is excited to have the opportunity to welcome a group of new and returning students to our facility this summer. Whether they are designing...
Sign up to receive the latest news from The Bradbury Group
Receive notifications when we update the used equipment list!